Strategic integration of Corporate Responsibility 2022
Breadcrumb
Strategic integration of CR 2022
Nested Applications
Strategic integration of Corporate Responsibility
Messer's activities are geared to the global economy, the environment and society, as well as to changes in these areas. In relation to the economic and social environment, we act sustainably and responsibly. We are also measured against our own objectives, innovations and traditions.
Climate change is increasingly altering the global conditions for living and doing business together - with direct consequences for people and companies. Accordingly, goals have been and are being realigned and market-economy framework conditions, including regulatory ones, are being adapted. For us, this poses risks, but also opportunities: we support our customers in taking important steps toward climate neutrality through our gas supply and gas applications.
In a social context, we attach great importance to diversity within our international team. Messer respects and promotes diversity, because we are convinced that with different strengths and ideas, we can implement even better solutions.
Long-term thinking and action, social responsibility towards employees and society as well as sustainable success - these are our central characteristics and at the same time our strengths as the world's largest privately owned industrial gases specialist.
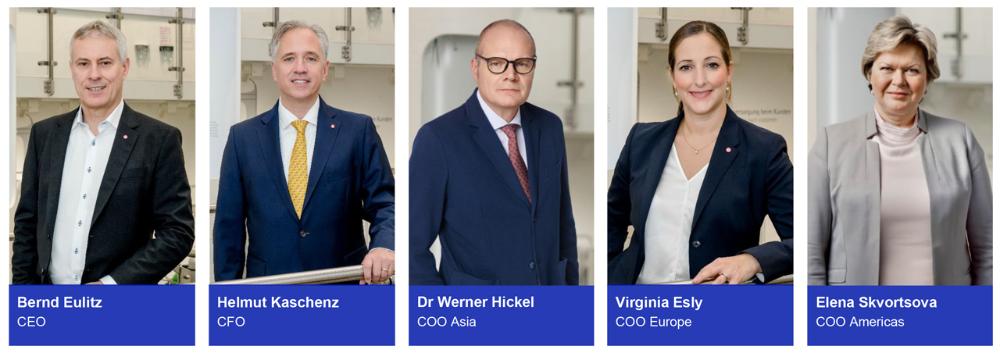
The Executive Board of Messer as of November 16, 2023.
The Management Board’s commitment to sustainability
As the world’s largest privately held company specializing in industrial, medical and specialty gases, we have clearly defined guidelines relative to ESG (Environment, Social, Governance), which are lived by everyone on our team. Our mission statement plays a key role here, combining our vision, our mission and our values. It also highlights the demands of our customers and our shared responsibility for the environment, people and progress.
Sustainability commitments of the management 2022
Environmental protection
Gases and know-how of Messer contribute to the UN's declared goal of achieving climate neutrality by 2050. To achieve this, we are minimizing our own carbon footprint and helping our customers to reduce CO2 emissions in their applications. This is made possible, among other things, by the impact of our gas applications and efficient gas supply.
We see green hydrogen as a lever for decarbonizing industry and mobility. Based on our H2 expertise, we are focusing on the particularly economical on-site generation of green hydrogen, on customized refueling solutions for hydrogen, and on an operator model for the use of fuel-cell-powered electric buses in local public transport.
Social entrepreneurship and diversity
The Messer team stands for courage, ambition, self-confidence, solidarity, success and respect. In 2022, we supported many social projects for people affected by the war in Ukraine through our "MesserAid" aid program, among other things.
Our diversity management is included in our strategic sustainability process via a key performance indicator (KPI). In 2022, we supported getting to know and understand each other in order to promote a respectful and unprejudiced culture at Messer.
We are consistently developing the potential of our international and multicultural teams. By 2030, we want to increase the proportion of female managers on the first and second management levels to 30 percent. Mixed management teams are a prerequisite for us to achieve balanced and profitable cooperation at a strategic level.
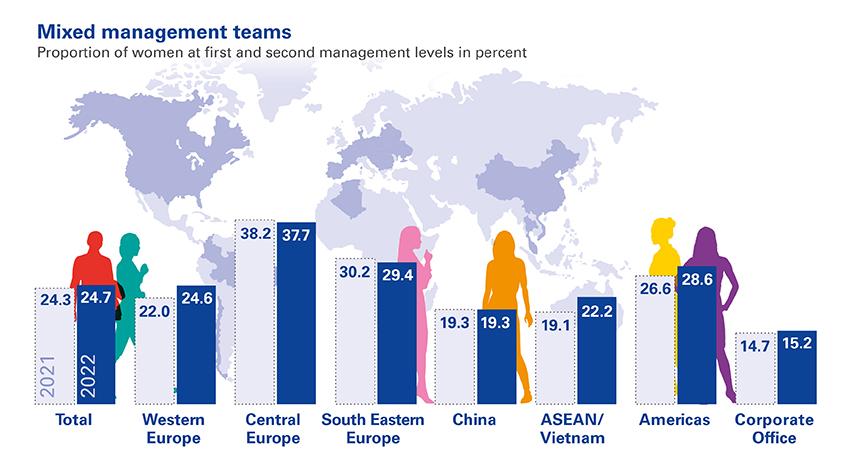
Governance
Messer is an international corporation that lives the values of a privately held company. The following corporate values undergird our commitment at all levels – from Management to Messer’s functional, specialist and production departments:
Integrity: We conduct our transactions with honesty and integrity, and expect the same of our employees, stakeholders and business partners.
Compliance: We comply with all applicable laws and regulations as well as our own values, internal guidelines and standards.
Responsibility: We hold ourselves accountable for our actions and decisions, and we expect our employees to do the same.
Continuous improvement: We endeavor to continuously improve our governance systems and our compliance performance.
Transparency: We communicate transparently with our employees, customers, stakeholders and other interest groups about our governance measures and successes.
Creation of our materiality matrix
The material topics of Messer's strategic sustainability process are determined by our daily and long-term activities. In addition, we are guided by the 17 sustainability goals of the United Nations.
To assess these topics, we involve as many of our stakeholders as possible and are guided by the requirements of relevant ESG standards and reporting frameworks, such as CDP, Ecovadis, GRI and SASB. We had managers and employees anonymously evaluate a list consisting of 14 topic categories and 80 individual topics regarding their relevance for Messer. Selected people from the areas of customers, suppliers, authorities, financial companies, politics, NGOs and journalism as well as followers of our social media channels also took part in the anonymous online survey.
The topics of safety, environmental protection, customer satisfaction and social responsibility were identified as the most important areas. We can influence all the key issues through our decisions. In addition, they potentially impact stakeholders outside the organization as well as the 17 UN Sustainable Development Goals. All material projects, both inside and outside the organization, are,therefore, relevant. In the following overview matrix, the assignment of our core topics to the UN Sustainable Development Goals is made clear by corresponding color coding.
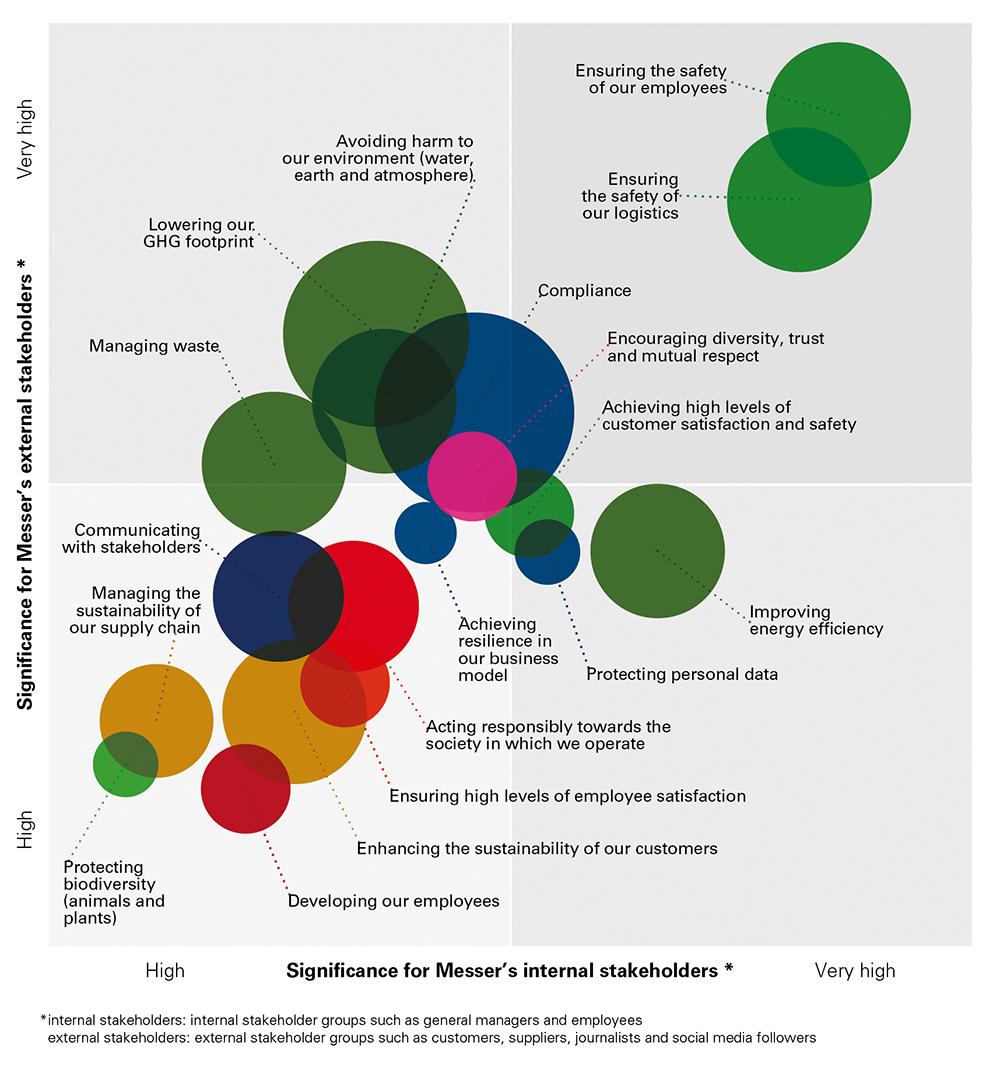
Internal and external stakeholders agree that we can make our greatest contributions to sustainability in the following topics:
- Safety: We are committed to the highest possible safety - for our employees as well as for our logistics and vehicles. The protection of data is a very high priority for us.
- Environment: We act in accordance with our compliance and continue to work on reducing our carbon footprint. We do not cause any pollution of water, soil or air. We conserve natural resources through the highest possible energy efficiency.
- Customer satisfaction: We meet the needs of our customers in terms of quality and performance, environmental compatibility, and plant and supply security.
- Diversity and equal opportunity: We operate based on diversity, trust and mutual respect, thus creating business advantages.
We focus on this as part of our continuous improvement processes.
Corporate responsibility
Our corporate values are anchored in a focus on customers and employees, responsible action, corporate responsibility, open communication, and trust and respect. To make these values and our development in terms of sustainable action measurable and comparable, we have been using key performance indicators (KPIs) for sustainability since 2014.
Through measurable targets, we document our improvements and developments in the various business areas. In this sustainability report, as in the financial year 2021, we are publishing harmonized key performance indicators relating to sustainability that reflect both groups of companies, Messer SE & Co. KGaA and Messer Industries.
This report is based on the UN Sustainable Development Goals and follows the G4 guidelines of the Global Reporting Initiative (GRI). In addition, we report to commissioned third parties such as EcoVadis, the Carbon Disclosure Project (CDP) and the chemical industry's Responsible Care initiative.
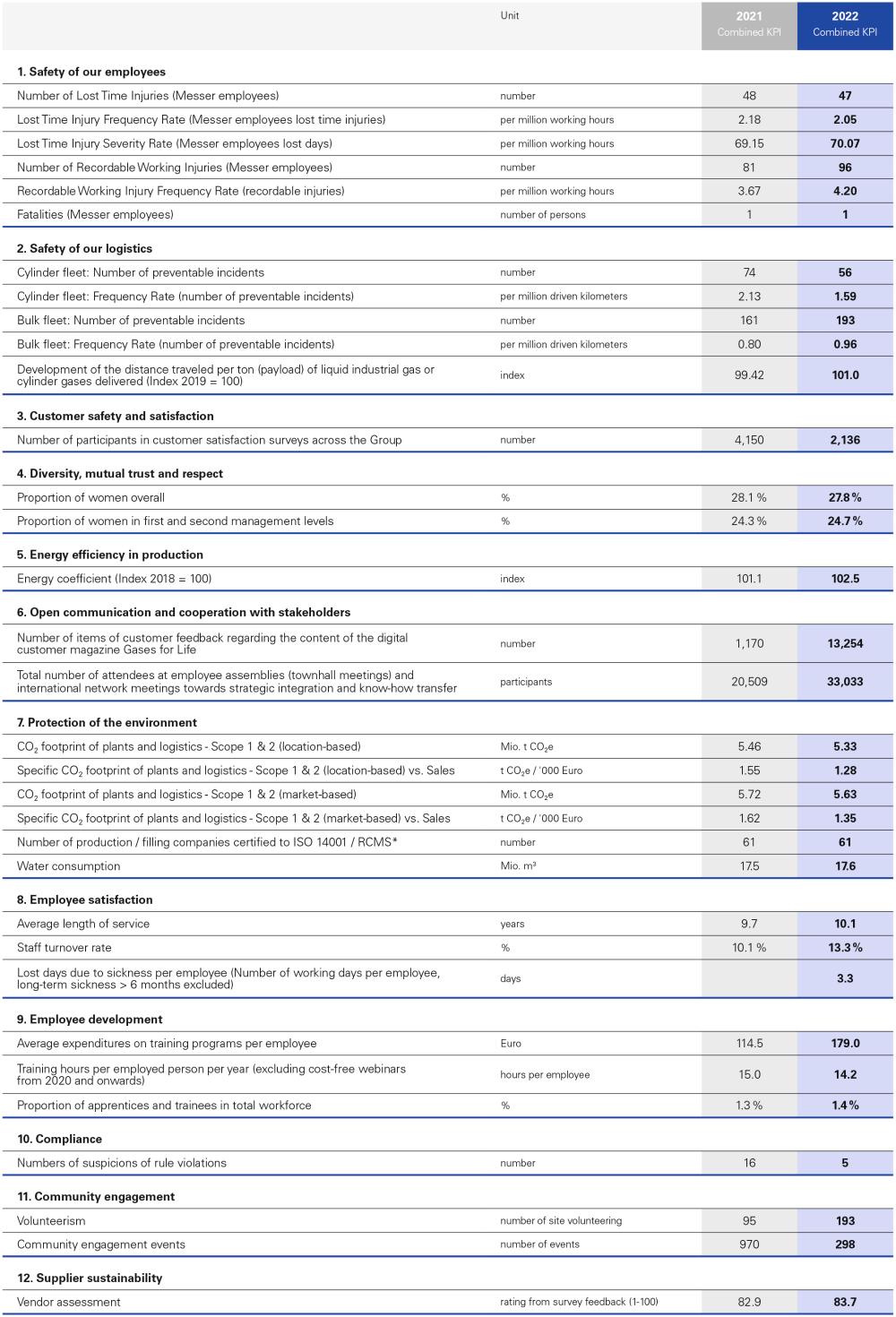
ORGANIZATIONAL AND PERSONNEL CHANGES
Bernd Eulitz appointed to the Management Board in 2022
On February 1, 2022, Bernd Eulitz assumed his new role as Deputy CEO at Messer SE & Co. KGaA. Previously, Bernd Eulitz was CEO in a German MDAX company. He looks back on over 20 years of experience in the industrial gases sector.
“The shareholders, Supervisory Board and Management Board are delighted to have won Bernd Eulitz, a person of integrity and an experienced manager from the industrial gases sector, for such an important position at Messer. His profound experience in the areas of international management and strategy will be very valuable in helping to shape the future of Messer as a continued successful, sustainable and diverse family business,” said Stefan Messer on the occasion of Bernd Eulitz’s appointment.
Bernd Eulitz has been appointed CEO of Messer as of April 26, 2023.
Helmut Kaschenz appointed as new CFO
In addition to his duties as Chief Sales Officer (CSO), Helmut Kaschenz has been appointed Chief Financial Officer (CFO) of Messer SE & Co. KGaA with effect from January 1, 2022. He took over the position from Dr. Uwe Bechtolf, who left the company at his own request on December 31, 2021. Before joining Messer, Helmut Kaschenz worked for 25 years in corporate and institutional banking in New York, London and Frankfurt/Main as well as in the chemical industry.
Virginia Esly appointed to the Management Board
On January 2, 2023, Virginia Esly was appointed to the Management Board as Chief Operating Officer Europe (COO Europe) for Messer’s European business. She has more than twenty years of experience in the industrial gases sector and is the first female Member of the Management Board in the history of the world’s largest privately held company specializing in industrial gases.
New manual for non-medical breathing gases
As part of the continuous improvement process, the Management Board of Messer SE & Co. KGaA adopted a new “Manual for Non-Medical Breathing Gases” within the Compliance Management System. It expands on the Messer Group Guidelines and supports the companies in their core obligations regarding legislation, standards and customer requirements. In addition, the manual defines Messer-specific requirements for non-medical breathing gases. It applies to companies in all European Messer regions that have customers in the field of non-medical breathing gases.
Revised version of the purchasing policy
The Corporate Logistics, Sourcing and Filling Plants department fundamentally revised the purchasing policy. The purchasing policy structures purchasing processes and procurement strategies to ensure that the goods and/or services purchased by Messer are the result of transparent, objective, time- and cost-efficient decision-making and risk management. The scope of application covers all Messer companies in Europe and Asia.
Revised purchasing policy for electricity
The Management Board of Messer SE & Co. KGaA approved the revised Purchasing Policy for Electricity within the Compliance Management System. The aim is to spread risks as widely as possible and increase planning security by means of a binding energy purchasing strategy. In addition, the policy contains a passage on covering electricity requirements via power purchase agreements (long-term electricity supply contracts between a renewable energy producer and a customer) as a further diversification component, but also as an essential factor in achieving the ESG targets that have been set.
Revised version of the Treasury Policy
The Group Treasury Department revised the Treasury Policy. The Treasury Policy has been adapted to the changed financing conditions and applies to all Messer companies in Central-Eastern Europe, South-Eastern Europe and China.
Corporate Responsibility
Messer Compliance Management System
The Messer Compliance Management System (Messer CMS) emphasizes our sustainable understanding of values. It is the binding framework for action to manage conflicts of interest and to comply with applicable laws, regulatory requirements and the rules and regulations of all Messer business units. The Messer CMS serves the goal of creating a relationship with our stakeholders that is based on fairness, solidarity and trust. It supports those responsible in establishing and implementing our value system. In addition, the Messer CMS is intended to prevent potential violations as far as possible in advance. Through their clear commitment, our managing directors and executives support the Messer CMS.
Messer Americas has signed up to the Code of Conduct and also uses its own Code Supplement as well as a Code of Conduct for Supplying Companies. Other guidelines include guidelines on compliance with competition law and anti-corruption, a compliance guide for business partners and a data protection guideline for North America.
Employees can report violations of applicable law or of the Messer Code ("compliance violations") as well as well-founded suspicious cases to the managing directors and managers at any time via the appropriate hotlines. These ensure that remedial action is taken immediately. In 2022, there were 5 such reports at Messer, compared to 16 in the previous year.
Speak up" compliance campaign
With a poster campaign under the slogan "Speak up.", Messer's management emphasized that it is expressly desired for employees to help uncover illegal or illegitimate conduct. Various reporting channels are available to them for this purpose, such as contacting superiors personally or using the whistleblowing platform Messer Integrity Line. The poster campaign also pointed out that employees who provide information about potential misconduct are protected. The posters were translated into the respective national languages by the local companies and displayed at many locations.
New concept for data protection organization
The Management Board of Messer SE & Co. KGaA adopted a new data protection concept. It is part of our Compliance Code and sets out the binding personnel and structural structure of data protection for all of Messer's fully consolidated European national companies. The new data protection concept contains the data protection statement, defines responsibilities and the basic data protection organization for the national companies.
Introduction of "multi-factor authentication" in Europe
In order to protect Messer's cloud services even better against cyber-attacks, multi-factor authentication (MFA) was set up for all Messer employees in Europe. Since then, employees who want to access Microsoft O365 from their Messer company location or mobile receive a sporadic request for an MFA.
IT security measures with first measurable successes
The results of the IT security assessment for Messer employees in Europe showed a slight improvement in 2022: overall, the frequency of errors fell and the score improved from 80 to 82 percent as of mid-October 2022. 33 questions from eleven areas had to be answered as part of the online IT security assessment. If the questions were answered incorrectly or inaccurately, the correct solution was displayed directly by the assessment platform. Based on the results of all assessments, a selection of training courses was assigned to the employees. The online platform remained open until the end of the year to give all employees the opportunity to complete their training or finish training, they had already started. In this way, IT security expertise was further strengthened.
Fourth European phishing simulation for employees
As part of the fourth European "phishing simulation campaign," Group IT Security sent a fake voice mail notification to 2,406 employees in November 2022. The result: the link in the phishing email to a fake voice message was clicked on by 10.8 percent (259 employees in total). This represents a downward trend of 7.1 percent compared to the previous simulation campaign. Employees who clicked on the fake link were assigned a training module on "phishing emails and dangerous links."
New tool for greater IT security
Cyber criminals often use emails as a gateway for their fraud schemes. To provide employees with technical support in the reporting process and in recognizing such emails, a phishing alert button was introduced in 2022, in parallel with the switch to Outlook Office 365. This allows Messer Group employees to simply forward a suspicious e-mail to a server with artificial intelligence. The reported, supposedly dangerous e-mail is analyzed there with the help of several intelligence and reputation systems. If the reported email is deemed dangerous, it is automatically moved from the Outlook mailbox to a quarantine and the affected employee is informed. This automatic analysis enables us to react even more strongly to IT threats and identify any trends.
Data protection
Messer is committed to complying with the applicable data protection regulations. Corresponding structures are in place to ensure a permanently high level of data protection.
The Group Privacy Officer of Messer SE & Co. KGaA is responsible for coordinating the central data protection department and supervising its implementation by the national companies. In accordance with the EU General Data Protection Regulation (GDPR) and the German Federal Data Protection Act (BDSG), we handle the data of our employees, customers, and business contacts in a legally compliant manner. Messer implements organizational and documentation measures specified by data protection law. To ensure optimum understanding, Messer's European national companies, and Messer SE & Co. KGaA communicate their data protection information in the respective national language via their websites.
Messer Americas complies with the applicable data protection laws, the related Code of Conduct of Messer SE & Co. KGaA for the Americas and the Messer Americas Code Supplement. In addition, Messer Americas has adopted a stand-alone Privacy Policy for North America. The Senior Counsel & Regional Compliance Officer of Messer Americas, the Head of Human Resources for North America Business Operations as well as members of the Messer Americas legal and compliance team are available throughout the Americas to answer questions regarding data protection. Messer Americas also makes use of external experts for compliance issues.
Training on data protection is included in the Messer Americas Code of Ethics and Conduct. The "Code of Ethics and Conduct" e-learning course is mandatory for all Messer Americas employees.
Sustainable, documented supply chain
A sustainable supply chain is a prerequisite for Messer's economic success. The relationships between Messer and its most important suppliers (key suppliers) are crucial in this respect.
The Logistics/Sourcing and Engineering/Production departments at Messer SE & Co. KGaA maintain contact with these key suppliers. They take over or provide central support for the Europe-wide purchasing of logistics services and commodities. The sustainable quality management systems of both departments are certified according to ISO 9001. Recurring audits of the key suppliers are an important part of their assessment.
The Production department supports Messer's national subsidiaries in the operation and maintenance of existing production facilities. The aim is to optimize production processes. Central computerized monitoring and control improves the profitability and energy efficiency of our plants, enabling us to continuously reduce the CO2 footprint of our plants. We are consistently implementing further optimization potential, revealed by regular process and energy audits.
The Engineering department is responsible, mainly in Europe, for the development and construction or conversion of plants for the production of technical and medical gases. In addition to plant design, project management, construction management and commissioning, these tasks also include the procurement or purchasing of all necessary plant components. The extensive experience gained from the construction and operation of existing plants is used to continuously improve the efficiency of our plants and to use technically high-quality, durable and energy-efficient components. Selected specialists work on the continuous further development of our processes. Among other things, they use current programs and software tools for process design.
Together with Messer Gas-Pack, the Logistics/Sourcing department ensures the availability and transport of gases of all kinds. This also includes the development of new logistics concepts as well as the roll-out and operation of optimization and control tools. In addition, purchasing activities are carried out or coordinated throughout Europe. This applies to tank trucks, customers' stationary tanks, evaporators, electrical power for production facilities, and gases from third-party sources. The leasing and recurring inspection of pressure vessels and fittings are another area of activity. In addition, the Logistics/Sourcing department supports the national companies in the management of transport contracts and the organization of heavy transports. On the one hand, the central processing of these specialist areas opens economic advantages, and on the other hand, high and uniform quality standards can be achieved across the board.
Supplier audits focus primarily on the production process, the quality of manufactured products and sustainability. Upon the key suppliers’ compliance with the principles of the UN Global Compact since 2018, the topics of sustainability, human rights, environmental awareness and working conditions have also been given the importance they deserve. In the event of an unsatisfactory assessment, we work together with the supplier company to develop appropriate improvement measures. Critical deviations, on the other hand, lead to a rejection of the company concerned.
Messer Americas also audits supplying companies on a regular basis.
Procurement focuses on material group management, strategic procurement and expenditure management within the procurement organization. Savings as well as the topics of health and safety are the focus here.
The Messer Americas Sourcing team combines expertise in the categories Indirect, Plants and Production, Merchant Packaged Gas, Customer Engineering Services, Logistics and Fixed Assets. It focuses on category management, contract lifecycle management, supplier relationship management and compliance. The sourcing team works closely with the operations team on all current investments. The Messer Americas Sourcing Team is governed by the Messer Americas Procurement Policy and the Messer Americas Procurement Guidelines.
Messer Americas Purchasing uses a supplier management system to ensure quality and compliance with standards relating to operational performance, safety, the environment, and social responsibility. Supplying companies are required to accept the Messer Code of Conduct statement as mandatory. In addition, Messer measures compliance with our standards in the USA by requiring compliance with our Conflict Minerals Statement and our Supplier Quality Statement.
The Messer Americas energy team manages Messer's electricity needs and, therefore, its largest variable cost. The dedicated energy professionals do this by working closely with the operations team to maximize benefits and efficiency. This is achieved by reducing electricity consumption during periods of high electricity prices or power grid emergencies.
In deregulated energy markets, the energy team has implemented a direct power procurement strategy. It allows Messer to purchase electricity directly from wholesale energy markets. In addition, the energy team utilizes an energy risk management program that has resulted in less volatile and decreasing electricity costs. In regulated energy markets, the energy team works closely with utilities, government agencies and other stakeholders. This ensures that Messer receives appropriate electricity rates based on operating costs.
The Messer Americas energy team cooperates with local, state and federal authorities. This is the basis for obtaining grants that reflect the operational flexibility and energy efficiency of Messer's facilities. Messer is also involved in various industry groups to help shape national and state energy policy. This is particularly true regarding topics such as green energy, sustainability, energy demand response and power grid resilience.